Unsere Automatisierungsstrategie
Wie schreitet die Automatisierung in den Warehouses voran?
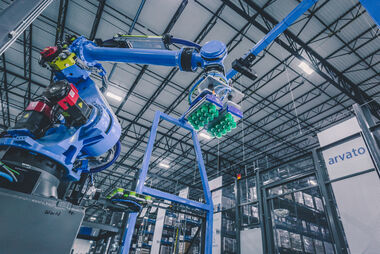
Philipp Rücker, Vice President Logistics Engineering, gibt einen aktuellen Einblick in die fortschreitende Automatisierung in unseren Warehouses und erklärt, wie wir die neusten Technologien und Innovationen finden, einplanen und welche Strategie eigentlich dahintersteckt.
Wie ist eigentlich der aktuelle Stand der Automatisierung unserer Standorte?
Die Automatisierung in unseren Lagern geht stetig weiter. Wir nutzen Technologien wie Ware-zur-Person-Systeme, einschließlich Shuttle, AutoStore oder Rack to Person bei denen Roboter die Ware automatisch aus dem Lagerbereich zu den Mitarbeitenden bringen. Diese Systeme steigern die Effizienz erheblich, entlasten unsere Mitarbeitenden und kompensieren den Arbeitskräftemangel. Externe Faktoren wie die Notwendigkeit schnellerer Durchlaufzeiten und die dadurch gesteigerten Erwartungen der Verbraucher, treiben die Automatisierung, insbesondere unserer Kunden im Bereich Fashion, Beauty & Lifestyle ebenfalls voran. Aktuell betreiben wir zehn AutoStores, sechs Shuttle-Systeme und setzen an sechs Standorten Automated-Guided-Vehicles (AGVs), also fahrerlose Fahrzeuge ein.
Ein besonders interessanter Bereich für die Automatisierung ist neben dem Transport die Verpackung, da wir durch maßgeschneiderte Kartons auf Abruf nicht nur die Effizienz erhöhen, sondern auch Verpackungsmaterial einsparen. Wir verschicken keine Luft und schonen damit die Umwelt. Der Betrieb vieler unserer Lager ist heute ohne einen gewissen Grad an Automatisierung schwer vorstellbar – von einfacher Fördertechnik bis hin zu vollautomatisierten Lagern mit Ware-zur-Person-Systemen, Robotern und AGVs für innerbetriebliche Transporte.
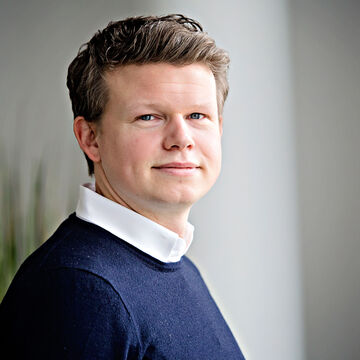
Wir treiben die Entwicklung unserer eigenen Warehouse-Control-Systeme zur intelligenten Steuerung und Vernetzung von automatisierten Subsystemen immer weiter voran, um die notwendige Transparenz zu schaffen und verschiedene Technologien und ganze Prozessketten zu automatisieren.
Philipp Rücker Vice President Logistics Engineering
VOR WELCHEN HERAUSFORDERUNGEN STEHEN WIR UND MIT WELCHER STRATEGIE LÖSEN WIR SIE?
Da viele unserer Geschäfte saisonalen Schwankungen unterliegen, verfolgen wir den Ansatz der „Human Technology Collaboration“. Wir automatisieren Bereiche wie Inbound, Pick und Pack, um die Arbeit für unsere Mitarbeitenden zu erleichtern und gleichzeitig Effizienzsteigerungen zu erzielen. Ein vollständig automatisiertes „Dark Warehouse“, in dem keine Mitarbeitenden mehr tätig sind, wird es bei uns als Logistikdienstleister mit hoher Flexibilität bei Auftragsschwankungen und der Art unserer Dienstleistungen nicht geben, auch wenn dies technisch bald möglich wäre. Unser Ziel ist es, über weite Prozessstrecken sogenannte „No-/Low-Touch-Prozessketten“ zu implementieren. Neben einer größtmöglichen Flexibilität für unsere Kunden versuchen wir auch immer die Drittverwendungsfähigkeit für andere Geschäfte zu berücksichtigen.
Welche unterstützende Rolle wird zukünftig die Künstliche Intelligenz (KI) im Warehouse spielen?
Roboter werden in immer mehr Prozessen und Lagern bei uns Einzug erhalten. Wir implementieren Lösungen von Boston Dynamics, Nomagic oder sogar selbst entwickelte Robotertechnik. Durch die Kombination mit KI und Vision Technology sind hier mittlerweile zahlreiche Use Cases in verschiedenen Produktkategorien möglich, z. B. in der Qualitätskontrolle von ausgehenden Sendungen aber auch bei Retouren.
Außerdem treiben wir die Entwicklung unserer eigenen Warehouse-Control-Systeme (Armada) zur intelligenten Steuerung und Vernetzung von automatisierten Subsystemen immer weiter voran, um die notwendige Transparenz zu schaffen und verschiedene Technologien und ganze Prozessketten zu automatisieren. Neben den komplexen Ware-zu-Person-Systemen werden wir versuchen, mit Autonomen Mobilen Robotern innerbetriebliche Transporte zunehmend zu automatisieren und sowohl wesentliche Inbound-/Outbound-Warenflüsse, als auch verschiedene automatisierte Sub-Systeme wie automatische Verpackungsmaschinen oder De-/Palletierroboter materialflusstechnisch zu vernetzen.
Wie werden geeignete Innovationen und neue Technologien gefunden?
Gemeinsam mit dem Future Warehouse Team und unseren Planungsteams, so wie dem Feedback aus unseren Standorten, definieren wir einen Innovations Funnel – hier versuchen wir, Trends und Technologien zu identifizieren, die erstens unser Portfolio ergänzen, zweitens einen wirtschaftlichen Vorteil für unsere Kunden bieten (z. B. besserer CPU) und drittens wiederholt in unseren Lösungen Anwendung finden.
Wie sieht der weitere Prozess aus, wenn diese Kriterien erfüllt sind?
Wenn es eine neue Technologie in unseren Funnel geschafft hat, durchlaufen wir folgenden Prozess:
- Wir scouten den Markt der möglichen Partner und entscheiden uns dann für 1-2 Lieferanten, die wir uns in einem zweiten Schritt näher anschauen.
- Durch Referenzbesuche hinterfragen wir die Qualität der Lösung und über tatsächliche Kunden Cases wird dann die Wirtschaftlichkeit der Lösung geprüft und ins Verhältnis zu bestehenden Lösungen gesetzt.
- Sollte die Lösung nach diesen Prüfungen weiterhin Relevanz haben, werden die Planer entsprechend durch die Hersteller der Systeme in der Kalkulation geschult und die Technologie wird in den Lagern ausgerollt und in unsere Benchmark Tools aufgenommen.