Our automation strategy
How is automation progressing in warehouses?
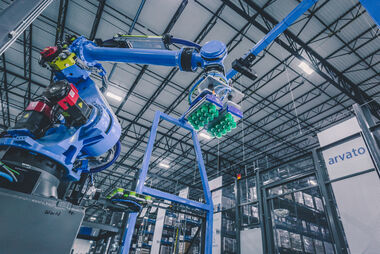
Philipp Rücker, Vice President Logistics Engineering, gives an up-to-date insight into the ongoing automation in our warehouses, an outlook on how we find and plan for the latest technologies and innovations, and what strategy is actually behind them.
What is the current status of the automation of our sites?
Automation in our warehouses continues steadily. We use technologies such as rack-to-person systems, including Shuttle and AutoStore, where robots automatically bring goods from the warehouse area to colleagues. These systems significantly increase efficiency, relieve our colleagues and compensate for the shortage of skilled workers. External factors such as the need for faster turnaround times, such as those imposed by Amazon with same- or next-day delivery, and the resulting increase in consumer expectations, are also driving automation. We currently operate ten AutoStores, six shuttle systems and use automated guided vehicles, i.e. driverless vehicles, at three locations.
Packaging in particular is an interesting area for automation, as we not only increase efficiency through tailor-made cartons on demand, but also save packaging material and protect the environment. The operation of many of our warehouses today is difficult to imagine without a certain degree of automation – from simple conveyor technology to fully automated warehouses with rack-to-person systems, robots and Autonomous Mobile Robots for internal transport.
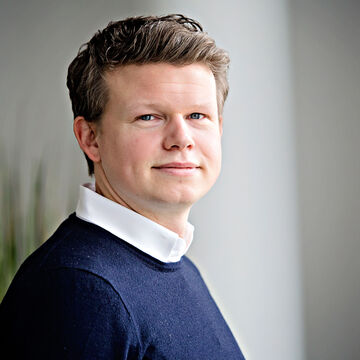
We are constantly driving forward the development of our own warehouse control systems for the intelligent control and networking of automated subsystems in order to create the necessary transparency and automate various technologies and entire process chains.
Philipp Rücker Vice President Logistics Engineering
WHAT CHALLENGES DO WE FACE AND WHAT STRATEGY DO WE USE TO SOLVE THEM?
Since many of our businesses are subject to seasonal fluctuations, we follow the approach of "Human Technology Collaboration". We automate areas such as inbound, pick and pack to make work easier for our employees while driving efficiencies. As a logistics service provider with a high degree of flexibility in order fluctuations and the nature of our services, we will not have a fully automated "dark warehouse" in which there are no longer any employees, even if this would soon be technically possible. Our goal is to implement so-called "no-/low-touch process chains" over long process stretches. In doing so, we strive for maximum transparency and flexibility, especially with regard to changes in product dimensions or container sizes.
What helpful role will artificial intelligence (AI) play in the warehouse in the future?
Robots will find their way into more and more processes and warehouses in the coming months. We are currently implementing solutions from Boston Dynamics, Nomagic or even self-developed robot technology. By combining it with AI and vision technology, numerous use cases in various product categories are now possible.
Here, we are also pushing ahead with the development of our own warehouse control systems for the intelligent control and networking of automated subsystems in order to create the necessary transparency and automate various technologies and entire process chains. In addition to the complex rack-to-person systems, we will try to increasingly automate internal transports with autonomous mobile robots and to network both essential inbound/outbound goods flows and various automated sub-systems such as automatic packaging machines or de-/palletizing robots in terms of material flow.
How are suitable innovations and new technologies found?
Together with the Future Warehouse team and our planning teams, we define an innovation funnel – here we try to identify trends and technologies that firstly complement our portfolio, secondly offer an economic advantage for our customers (e.g. better CPU) and thirdly are repeatedly used in our solutions.
What does the further process look like if these criteria are met?
When a new technology has made it into our funnel, we go through the following process:
- We scout the market of possible partners and then decide on 1-2 suppliers, which we take a closer look at in a second step.
- Through reference visits, we question the quality of the solution and the profitability of the solution is then checked and compared to existing solutions via actual customer cases.
- If the solution continues to be relevant after these tests, the planners are trained accordingly by the manufacturers of the systems in the calculation and the technology is rolled out in the warehouses and included in our benchmark tools, such as our de/palletizers or rack-to-person systems.