Paperless Logistics
How do standardized digital paperless processes help us and our clients to reduce carbon emissions and costs?
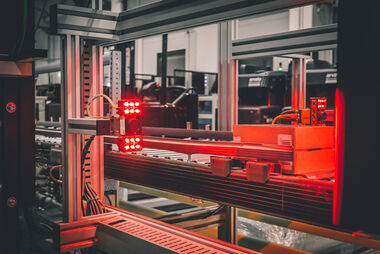
We interviewed our colleague Dr. Jens Muth-Böhm, who works in our Digital Acceleration Team, which creates value for our clients and their end customers by using digitalization to increase operational efficiency.
Can you give us a brief introduction of what the Paperless Logistics initiative is all about?
There are two main reasons to set up this initiative: First, sustainability is becoming more and more a priority for our clients, and we at Arvato have also announced an action plan to become carbon-neutral by 2030. Second, paper-based processes are inefficient and costly due to the use of consumables, the accompanying productivity and their high vulnerability due to dependence on printer infrastructure.
Therefore, our Paperless Logistics Initiative aims to digitize all high-volume documents that are printed repetitively and optimize related logistic processes. This includes end customer documents e.g. invoices and delivery notes as well as documents used in warehouse processes e.g. picklists or loading lists.
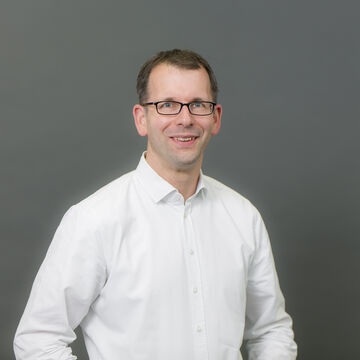
Our Paperless Logistitics Initiative offers us the opportunity not only to save paper and energy and thus have a positive impact on our sustainability goals, but also to save costs.
Dr. Jens Muth-Böhm Director Digital Projects
How is the digitization of end customer documents integrated into existing logistics processes and how does it contribute to sustainability?
Imagine a B2C order where an invoice, a delivery note, a return document and a return label are printed and enclosed with the parcel. Given the large number of annual B2C orders, companies print millions of pages every year, which can be avoided through digitization: End customers can then receive these documents by e-mail or simply download from their customer area of the web shop. This is why end customer documents are an important focus of our initiative.
To digitize those documents, we have set up a Document Management System (short ‘DMS’), which is an orchestration of services we have already in place (e.g. an audit-proof archive) plus a solution to provide these documents digitally to end users. The provision of these documents can be easily integrated in existing logistics processes since the DMS is directly coupled to existing infrastructure like SAP or warehouse services.
What impact does digitization have on the efficiency and accuracy of our logistics processes?
Paperless makes logistics’ life easier. There will be less GDPR-related issues and fewer complaints due to transparent and accurate customer communication. Logistics processing times can be shortened, they become scalable and adaptable to upcoming changes in the business. Just think about the packing process: The employee no longer has to wait for printed documents (e.g. an invoice) and then place them in the parcel by hand before sealing it.
Are there any challenges that arise when converting to digital end customer documents? How can these be overcome?
Yes, there are some. Our clients are often concerned that without paper invoices the number of defaults and customer service inquiries will increase. But our facts and figures simply do not prove this concern for clients switching to paperless. Of course, such a change must be managed carefully and communicated well in advance to overcome the initial concerns.
Next to that, sustainability strategies driven by our clients usually focus on the manufacturing process. By referencing and showcasing similar brands, we and our ESG experts, advise clients to consider all aspects of becoming more sustainable – also their supply chain.
What benefits do our clients expect from the digitization of end customer invoices/documents?
Benefits arise at various levels: Sustainability gets a boost by avoiding unnecessary consumables. Cost savings can be raised due to less consumables, less investment in printer infrastructure and a reduction in process times. And finally, the end customer profits from a perfect and lean customer experience. As the whole e-commerce industry is currently drifting to entirely paperless processes, many customers themselves now demand fully digital services.
Can you briefly explain how the ‘Customer Experience Cloud’ fits into the Paperless Logistics initiative and what it is all about?
The ‘Customer Experience Cloud’ (CXC) is Arvato’s digital product to enhance the post purchase experience for end customers of our clients. One of the key services is the ‘Online Returns Center’, a fully managed and integrated service that allows end customers to digitally register their returns. The option to generate a QR code for carrier- and even retail returns makes pre-printed return labels obsolete.
Furthermore, other return documents can be eliminated because all relevant information is provided by the digital return registration. For a fully consistent digital experience, the digitization of invoices and delivery notes using the document management system is vital part of our offering.
Can you give us a few examples of paperless first movers at Arvato? And can you give us some figures that show the impact of paperless logistics?
One of our clients, a German shoe manufacturer serving the European market, has switched completely to paperless: both for end customer as well as for warehouse process documents. Another client, a European market leader in fashion, went fully digital for end customer communication, saving 2.2 tons of paper - per week!
A Japanese manufacturer of electronic components proactively adopted the paperless approach for B2B orders. Its customers can configure which documents are required in paper form and which can be provided digitally. This enables a massive savings potential.
Other clients rely on hybrid solutions: documents are provided digitally and paper-based with the goal of avoiding paper in future. The aim of the brands here is to gradually and carefully adapt customer behavior.
Outlook and your call to action: How do you envision the future of paperless logistics and the digitization of processes in terms of sustainability? What further steps are you planning to take to advance digitalization in logistics?
We have already achieved a lot – but we're just getting started. I am pleased that the processes for new Arvato businesses are designed to be as paperless as possible and that changes are increasingly driven within the organization by the aim of saving paper. All in all, this initiative offers us the opportunity not only to save paper and energy and thus have a positive impact on our sustainability goals, but also to save costs.
However, a lot of persuasion work still needs to be done on the end customer documents, and that takes time. Our strong collaboration with our ESG representatives at Arvato is helping us to spread the message. Going paperless can be a real game changer for our sustainability strategy and – equally important – our financial performance. It is never too late nor too early to kick-off the transformation.
What can our employees do to further facilitate the mission of becoming a fully paperless running logistics company?
A lot. This starts on a small scale: often the use of paper can be avoided from an organizational point of view. Ask yourself if a certain document really needs to be printed. And talk to the business owner or account manager about ideas to digitize the process.
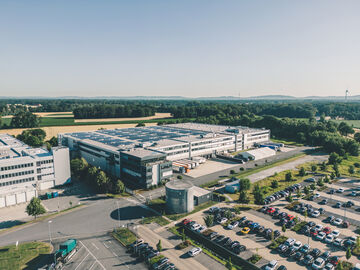
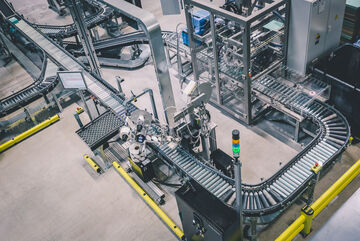