Nasze innowacyjne wewnętrzne rozwiązanie robotyczne
Arvato z dumą prezentuje "Leleka", zaawansowane ramię robotyczne zaprojektowane do automatyzacji kompletacji i sortowania artykułów modowych w środowiskach magazynowych.
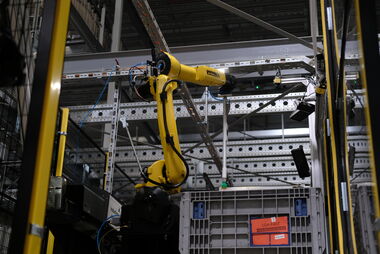
Robot wykorzystuje możliwości wizyjne napędzane przez sztuczną inteligencję, aby automatyzować proces rozładowywania pojemników zbiorczych zawierających po kilkaset pozycji odzieży. Dzięki wysokiej precyzji i dokładności w podejmowaniu decyzji, realizacja zadań jest niezawodna i efektywna. Zintegrowany z systemem BagSorter w Hanowerze, robotyczne ramię identyfikuje optymalne miejsce do chwycenia każdego produktu, zapewniając bezpieczny i wydajny ruch. Sprawdza widoczność produktu, jego aktualne położenie względem innych oraz czytelność kodów kreskowych, radząc sobie z nieregularnie ułożonymi produktami losowo w pojemnikach.
Główną motywacją wdrożenia Leleka było odciążenie pracowników od najbardziej monotonnych i nużących zadań, takich jak przekładanie produktów w magazynie, a w obliczu rosnących wolumenów, rekrutacja nowych pracowników do podstawowych procesów logistycznych staje się coraz trudniejsza. Łącząc ramię robotyczne z algorytmami AI opartymi na przetwarzaniu obrazu, Leleka jest zaprojektowana do obsługi skomplikowanych procesów z wyjątkową precyzją, poprawiając jakość naszych operacji. Leleka idealnie wpisuje się w naszą strategię automatyzacji i służy potrzebom biznesowym naszych klientów.
„Leleka oferuje długoterminowe korzyści finansowe, odpowiada na braki kadrowe i odciąża pracowników poprzez automatyzację rutynowych zadań. Zwiększa stabilność i efektywność operacyjną, wspierając procesy logistyczne Arvato nawet przez całą dobę”, mówi Sławomir Grzeskowiak, szef zespołu R&D Arvato, który opracował system Leleka.
Leleka działa z wydajnością na poziomie co najmniej równym wydajności człowieka, lecz bez spadków produktywności spowodowanych zmęczeniem. System jest zoptymalizowany do pracy 24/7, zapewniając ciągłość operacyjną. Działa autonomicznie, z minimalną ingerencją pracowników w takie zadania jak wymiana pojemników zbiorczych, lecz w przyszłości planuje się automatyzację również tego etapu. Personel techniczny otrzymuje specjalistyczne szkolenie w zakresie uruchomienia początkowego urządzaenia, codziennego monitorowania pracy i prostych zadań konserwacyjnych.
„Rozwój Leleka stanowił znaczące wyzwania, szczególnie w zderzeniu teorii z rzeczywistością. Produkty, nigdy nie są idealnie ułożone w pojemnikach zbiorczych, co wymagało dostosowaniu się do nowych warunków w oparciu o wiele kryteriów. Dzięki rygorystycznym testom i adaptacji rozwiązania do istniejących warunków nasz zespół projektowy pomyślnie sprostał tym wyzwaniom, zdobywając cenne doświadczenia i ogromne ilości danych do przyszłych wdrożeń”, wyjaśnia Grzeskowiak.