Integration of a shuttle system in Harsewinkel
Fabian Generotzky is Director Operations at the Harsewinkel site and is responsible for the smooth running and further development of daily business operations. In this context, he is also the project sponsor for the current project - the integration of a shuttle system! As part of the rebuild at the Harsewinkel site, Fabian is keeping track of things - we asked him what's important in the process.
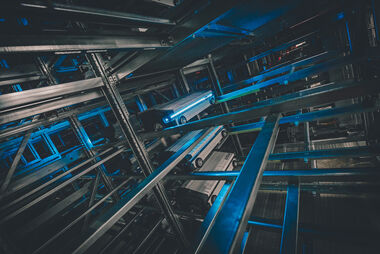
What are the challenges when such a large project is/will be implemented during ongoing operations?
At the Harsewinkel site, we support a total of around 40 healthcare clients with their individual requirements. Especially with the long project duration of approx. 12 months and the strict schedule, it is necessary to resort to interim solutions. Since large parts of the facility had to be rebuilt and cleared, it was unavoidable to move the storage areas and deliveries to replacement areas. Construction site operations are currently part of everyday life and we have to act accordingly.
It is mandatory that daily business continues without disruptions and patient care is guaranteed!
Fabian Generotzky Director Operations
Is there anything that needs special attention? How do you handle these special features?
In fact, there are many dependencies that can be well traced in the project plan and that show that really all areas and halls are part of the project in different forms.
One example is the conversion of the former ambient area (15-25 °C) in HW3 to 2-8 °C. Before the hall is released for pharmaceutical products in the new temperature range, it must be proven via a so-called mapping phase that the specified temperature range is also maintained. This proof is provided by several hundred loggers that record the temperature over a period of two weeks.
If a logger registers a temperature deviation outside the specified range during this mapping, the mapping must be repeated in the worst case. The sensitivity of the measuring devices is so high that, under certain circumstances, even an accidentally opened outer door can lead to a corresponding temperature deviation.
The delay caused by a missing release and a necessary remapping could then result in moves into the area not being able to take place as planned. Accordingly, there is no construction clearance in the areas that are to be cleared, and the tightly timed project schedule falls behind schedule. This once again highlights the complexity of this project.
To ensure that we can act as accurately as possible here, we take an incremental approach. Subprojects are considered individually, always with a view to the critical schedule and in the context of the overall planning, in order to identify problem areas early on and initiate countermeasures.
Fabian Generotzky Director Operations
What is the best way to manage a project like this so that there are no delays? Is there a plan B?
Patient care remains the top priority. This must be maintained and is the top priority, so that any risk to the patient from a delay is ruled out.
The advantage we have here is the high number of clients. A total of 26 will move to the new system. This allows us to transfer individual clients from the replacement areas to the shuttle step by step. In doing so, we can react to any unforeseen circumstances and create solutions. Accordingly, we are also planning a fallback scenario so that we can jump back to manual processing during the go-live in order not to jeopardize the ability to deliver (= patient care).
The complexity of the project indicates a high number of stakeholders. Who is actively involved and how do you keep track?
There is no department internally that is not affected. Starting with IT, which is responsible for the technical connection, through the quality department, construction, and transport department, to logistics engineering as well as operations, key account managers and marketing. All of them are part of the project and must be constantly informed about the status or are actively involved in subprojects.
In addition, there are external stakeholders who also play a significant role in successful implementation. In addition to the clients, the district government in Detmold is one of these, because it is only through the auditing of the authority that the use of the newly created automation option is possible. This gives us permission for the use of the hall and the associated storage of medicines. Furthermore, other service providers, such as the construction site trades or suppliers, are also an important part of the project. Due to the very tight project schedule, even the smallest delays can cause an entire project to be delayed. The right coordination and communication are crucial here.
What do clients have to be prepared for?
We keep the risk for our clients to a minimum. We create transparency through regular and detailed communication. The general background as well as motives with the advantages of the realization of the project are known and individual queries are answered by the key account managers. In addition, the quality department is in constant exchange with the quality departments of the clients. The challenge here is that communication runs in parallel and all parties involved need the same level of information. This is important for good cooperation and trust.