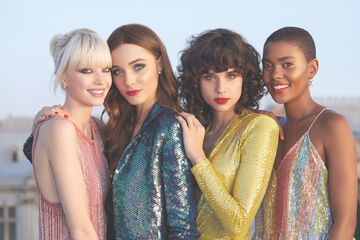
Client Success Story | Douglas
More than 20 years of partnership go into the next round

For Douglas Group, we handle the entire B2C and B2B volume of the DACH region from our new, highly automated location. In this way, we support our clients's growth and strengthen its omnichannel positioning at the same time.
The initial situation
As Europe's leading omnichannel provider for beauty, DOUGLAS Group is active in both e-commerce and brick-and-mortar retail and has grown continuously over the last nine fiscal quarters. We have been working in partnership with DOUGLAS Group for over 20 years. To enable current and future strategic growth, it needs a scalable, cross-channel fulfillment solution for the omnichannel retailer's entire product portfolio.
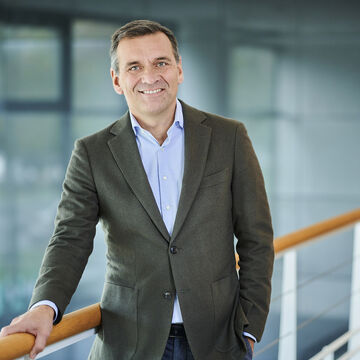
Efficient logistics is one of the most important pillars for any omnichannel retailer. With the new and state-of-the-art logistics center in Hamm, we have reached a decisive milestone in linking store business and online store in the DACH region even more closely - also and especially to the benefit of our customers and suppliers.
Sander van der Laan CEO Douglas Group
Our solution for success
To best support Douglas Group in its growth objectives, we have expanded our fulfillment solution, taking our partnership to the next level: In 2022, we opened our highly automated location in Hamm, from where we cover all B2C and B2B logistics within the DACH region.
From goods receipt to shipping - in addition to classic services such as warehousing, picking, and packing, we take on value added services and returns processing. In value-added services, we support Douglas Group set formation and serial number handling.