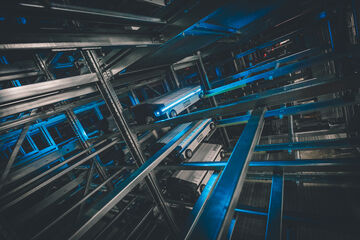
Partner Success Story | KNAPP
Optimized omnichannel logistics for beauty products
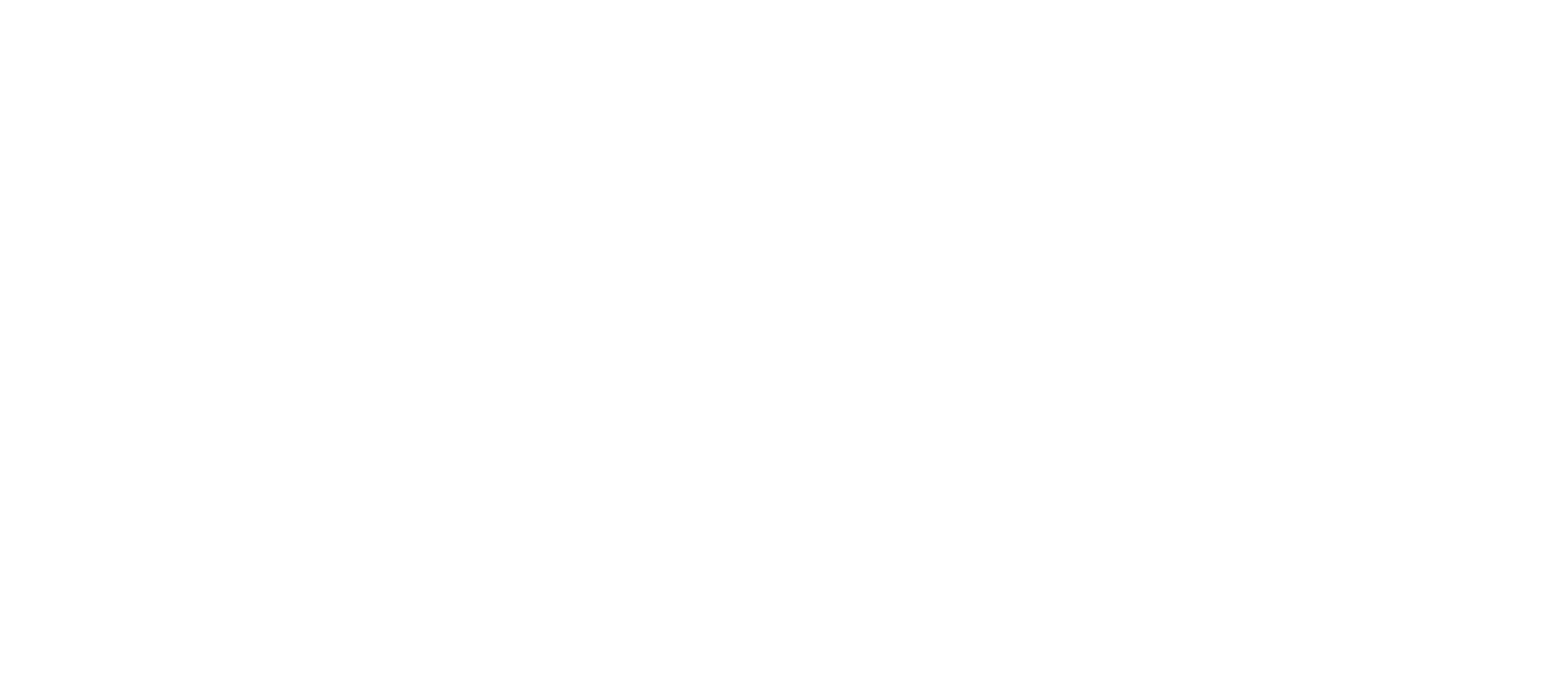
We enable higher throughput for B2B and B2C on a conveyor line while ensuring the flexibility required for online business, by using a shuttle system.
The shuttle system is designed for future growth and optimized for seasonal peaks
Together with KNAPP AG, a total solution provider for intralogistics and automation solutions, we have developed a holistically optimized omnichannel supply chain concept for our client, the DOUGLAS Group. At the heart of the new, highly automated warehouse in Hamm is the KNAPP Evo Shuttle 2D, a shuttle system with 550 shuttles.
The Challenge
The DOUGLAS Group is Europe's leading omnichannel provider of premium beauty and has a total of around 400 stores in Germany, Austria and Switzerland. Together with Arvato as logistics and fulfillment partner, the group has pursued a successful growth course for more than 20 years. However, especially due to the strong growth in e-commerce business, the shipping volume has risen continuously in recent years. Since around 32,000 orders per hour were received via all systems at peak times, the DOUGLAS Group decided on a holistic omnichannel strategy in order to interlink the branch and online business even more closely and thus optimize the customer journey. At the heart of the new solution is our omnichannel hub, which, in contrast to the decentralized approach, enabled higher availability of products with a shorter delivery time.
To do this, the existing logistics concept had to be revised, which consisted of a fulfillment center for e-commerce and five cross-docking centers for deliveries to the stores for the DACH region. An additional challenge was the diverse range of products offered by the DOUGLAS Group. Changing trends regularly influence the product range and its availability and therefore require the most flexible approach to warehousing.
The solution: By using a shuttle system, we enable higher throughput for B2B and B2C on a conveyor line while ensuring the flexibility required for online business.
World's largest 2D shuttle solution in the cosmetics sector
550 2D shuttles are in use in our 38,000 square meter warehouse in Hamm, which we have built as a new omnichannel hub for the DOUGLAS Group. The KNAPP shuttles function as a flexible small parts warehouse and bundle relevant storage processes such as the storage and retrieval of containers or the efficient storage of inventory and excess stock. Buffering and sequencing as well as replenishment for other work areas are thus handled very easily. The shuttles move independently between 22 aisles on 25 levels and bring the required goods in containers to one of the 32 technology-supported goods-to-person workstations. Further picking steps are also handled by pick-to-light. The automation solution offers a range depth of 80,000 SKUs and a storage capacity of 8 million units on stock.
Man and machine work hand in hand
Many products from our client's range are highly flammable and have different sizes and weights. For this reason, they are not suitable for picking by an A-frame picking system, which is popular in the beauty sector, or for automated separation in the decanting process. These activities are carried out by our employees. Our teams also fill shipments with free samples. Around 700 samples per person are added per hour - a robotic solution would only be able to manage 500 samples in the same time. For special items such as promo boxes or Advent calendars, there are separate stations from which they go into the shipping process. Value-added services such as flyers, on the other hand, are automatically added to a shipment. The erecting, closing and labelling of the cartons is also done automatically. Up to 114,000 parcels leave our warehouse every day.
It is precisely in times of great challenges that the true strength of a partnership becomes apparent. Together with Arvato and the DOUGLAS Group, we have proven that we can harmonize and achieve great things even under pressure
Hannes Kracher Head of Sales and Key Account Manager for Arvato at KNAPP
Increased productivity and product availability
Through our new, centralized warehouse and the implementation of the KNAPP 2D shuttles, we were able to significantly increase the performance of the logistics concept for the DOUGLAS Group. Delivery times for the approximately 400 stores have been reduced from twelve to four days. Thanks to its scalable design, the automation solution is also geared towards the coming growth of our client and is optimized for seasonal peak times such as Black Friday or the Christmas business. "KNAPP acts as a constant for us with which we can improve together and always supports us in achieving our strategic goals with its future-oriented solutions," says Sebastian Altrogge, Key Account Manager at Arvato. The joint cooperation with KNAPP began back in 2011 – since then, nine tailor-made projects have been jointly implemented for clients in various industries.